Case Study: Synerion WFM Solutions at Palram Industries
About Palram
Palram Industries Ltd. is a leading global manufacturer of thermoplastic panels, architectural roofing and cladding systems, and finished products for self-assembly. Palram panels are made mainly of polycarbonate and PVC in extrusions and are suitable for a wide range of applications in construction, architecture, agriculture, graphics & display and DIY.
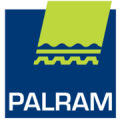
architecture, agriculture, graphics & display and DIY.
Founded in 1963, Palram became a publicly held company in 1994. In the field of polycarbonate panels, Palram is one of three leading companies in the Western world in terms of production and sales, alongside companies such as SABIC and Covestro (formerly Bayer). Palram estimates that its global market share in the field of polycarbonate (in the Western world) is about 10%. In the field of PVC sheets, Palram is a well-known and reputable worldwide manufacturer.
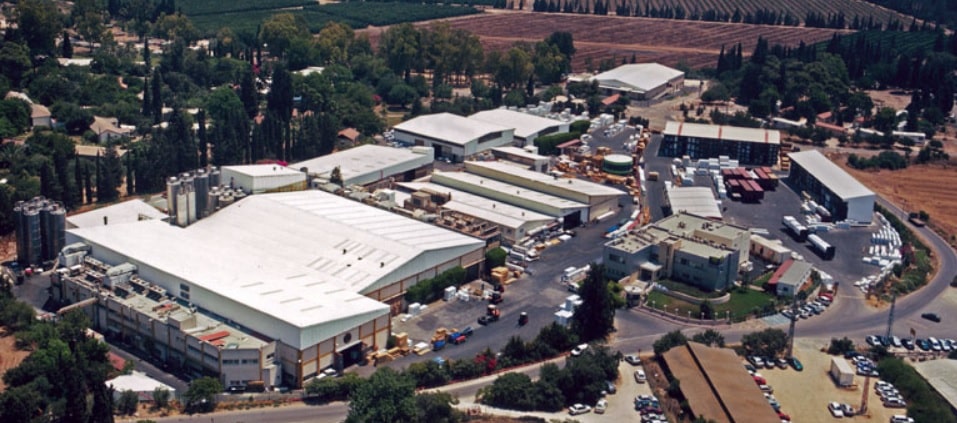
Palram headquarters and main production plant are located in Kibbutz Ramat Yohanan in Israel. Additionally, the company has sales offices and plants in Europe, America, Africa, Australia and Asia.
In Israel Palram has 500 employees under a variety of labor agreements: hourly, monthly, global, shift, etc. Its production departments operate 24X7 in three shifts.
The Challenges
As a labor-intensive organization with a variety of employees, most of whom are shift workers, managing attendance was complex and required manual report updates by the end of each month, creating huge bottlenecks at the HR department prior to payroll preparation.
The endless pursuit of employees with incomplete reports and managers who had to correct reports and approve overtime, led to the decision to provide managers, even line managers, with tools to plan, manage and monitor their employees’ shifts, attendance and absences in real time, while complying strictly with labor laws and employee rights.

The Solutions
Palram is a long-time customer of Synerion’s workforce management solutions. However, up until the latest version of the system, only some departments used the manager self-service tool to manage the attendance of their employees. As a matter of fact, at that point in time the system was not used regularly as a daily tool.
In order to improve management, control and monitoring capabilities, the system was upgraded and new modules were added.
Synerion Direct – Manager Self-Service
As part of the upgrade process, it was decided that HQ employees and plant managers, starting with line-managers, will use Synerion Direct, the self-service tool, to update their own and their teams’ attendance reports, as well as manage absentee requests. The organizational tree was changed to feature more details, identifying each employee’s supervisor responsible for managing, updating and monitoring issues of attendance, overtime, etc. on an ongoing basis.
The day-to-day use of Synerion Direct, the self-service tool, enables employees and supervisors to take responsibility for such issues, thus preventing bottlenecks at the payroll department, at the beginning of each month.
“The process of completing missing data at the end of the month has become simple: instead of 3 days of madly racing to finish piles of paperwork, all processed and approved information is automatically transferred to the payroll department no later than 12:00 noon by the 2nd of each month.”
Hasik Barber, HR manager, Palram Israel
Absence Management
The Synerion Absence Management system was also added during the upgrade. The system provides managers with a comprehensive view of their employees’ time-off balances, as well as previously approved absences, allowing them to make an informed decision as to whether the request for additional absences can be approved without compromising the proper coverage for workloads. Here too, making the process the managers’ responsibility has made it simpler. Employees turn to their team leader, who determines whether to approve / reject a request, without having to go through the HR department.
Scheduling and Alerts
Another significant addition to the upgrade was the Scheduling system for the production floor that operates in three shifts, 24X7.
Up to that point, managers used paper/Excel to plan their employees’ shift schedule for only a week ahead. The work schedule was determined according to a basic template: two days morning shifts, two days evening shifts, two days night shifts, and two days off.
Immediately after the weekly work schedule was printed and posted on the notice boards, workers began to change and shuffle shifts. Soon after, the work schedule was no more than a table of scribbles.
With the introduction of the Synerion Scheduling system, the process became far more manageable. It is now prepared two weeks in advance, enabling both managers and employees to plan ahead and organize better. A manager can easily identify who can replace an employee who is not available for a particular shift without having to breach labor laws. The Synerion Alerts system blocks the allocation of a worker to a specific shift if there is a possibility of non-compliance with labor laws, and provides alerts about employees who are reaching the overtime quota permitted by law.
Payment to the employee is determined by his work schedule and not his punching-in time. Today, any shift swap is automatically reflected in the system, as well as in the payroll calculation, without the need for retroactive corrections.
“The introduction of the Synerion Scheduling system was designed to plan the work scheduling in a more structured and orderly manner. The challenge was to harness managers and employees to the process, and we were certainly successful in what we wanted to achieve. Since the transition to the Synerion Scheduling system, the number of changes, both by managers and employees, has decreased significantly”,
says Hasik Barber, HR manager, Palram Israel.
“Overtime is now managed and monitored. Managers have a clear view of their employees’ actual overtime and overtime quota utilization. They can find the reasons for any irregularities, and unhesitatingly decide what to approve and what to decline.
At the end of the process, all information is transmitted systematically to the payroll department for an accurate calculation of the payroll.
I, myself, use the Control Panel (dashboard), which allows me to easily identify anomalies, alerts or anything that needs my attention, including its drill down capabilities, to identify the root of a problem. In addition, now I know who is available in case of emergency”.
The Benefits
- A variety of day-to-day tools that enable managers to plan, monitor and update information
- Transfer of workforce management responsibilities to managers and supervisors
- More agility and increased operational effectiveness
- Compliance with labor laws and regulations
- Information-based absence approval to prevent understaffing
- Simple preparation of all information required to accurately calculate payroll
- Real-time employee attendance information
- Reduction of paperwork and administrative efforts in the Payroll and HR departments.